Macro Keyboard
Introduction
The goal for this project was to take a product from an initial idea all the way through prototyping, DVT, and PVT stages. The team would have to focus on DFMA and focusing on real world manufacturing techniques. Additive manufacturing was allowed for the initial prototyping stages, but beyond that it was prohibited due to real world implications of mass production.
My idea for a project revolved around creating a small keyboard dedicated to providing the user with buttons that provide shortcuts to valuable functions in a variety of applications. This would provide the opportunity to make a genuinely useful and functional device with a strong emphasis on design. It would also give the team the opportunity to tackle a variety of manufacturing challenges.
Concept Development
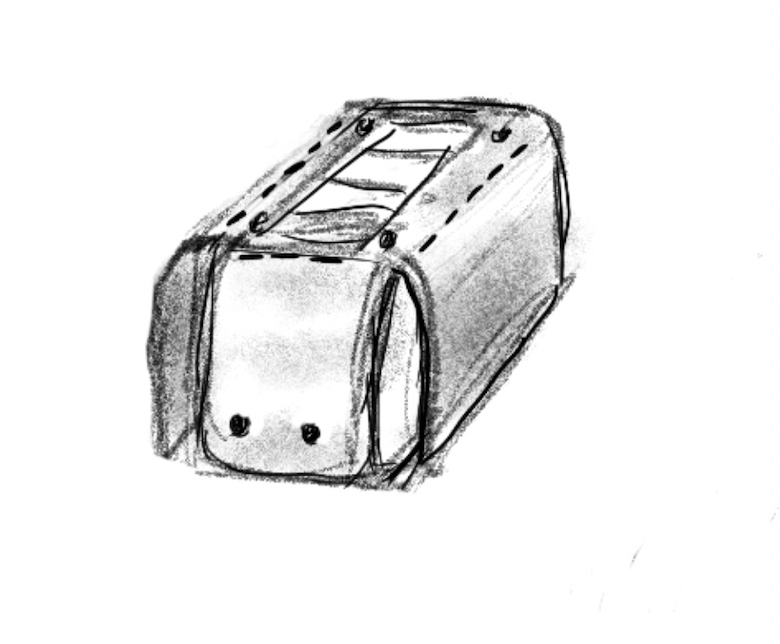


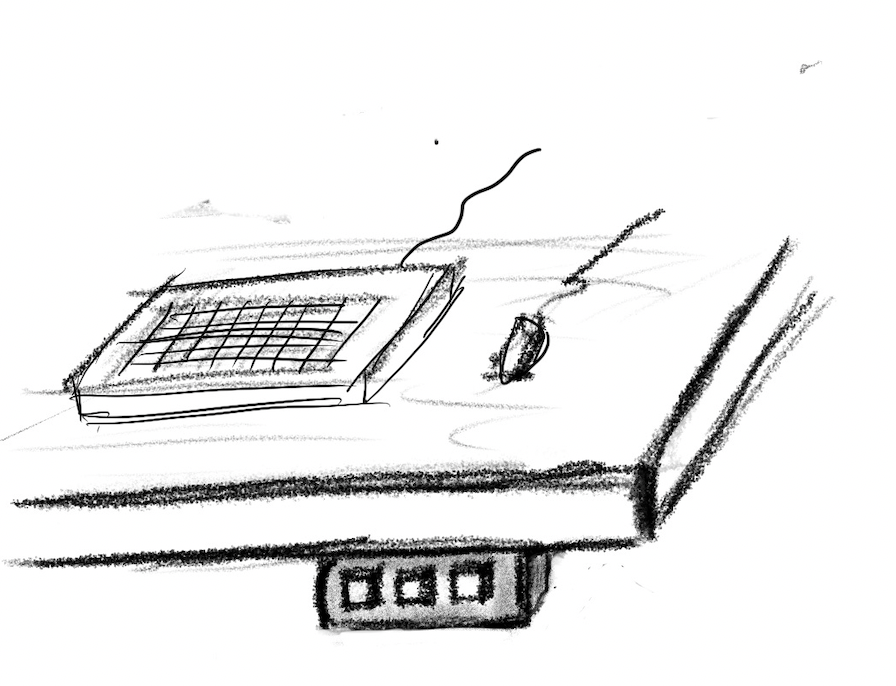
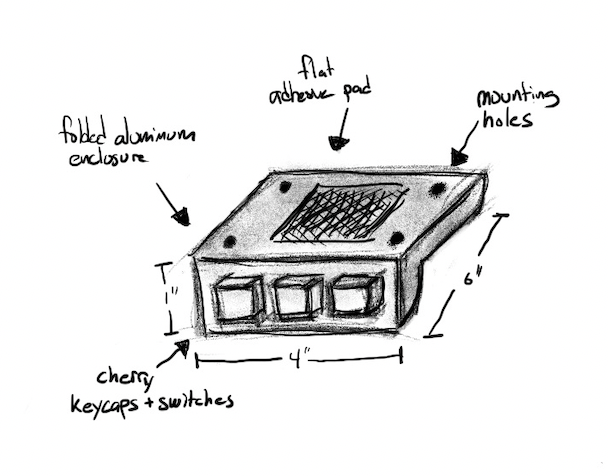
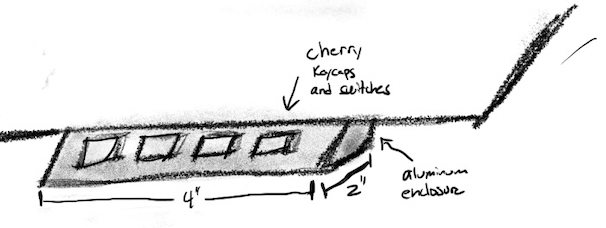
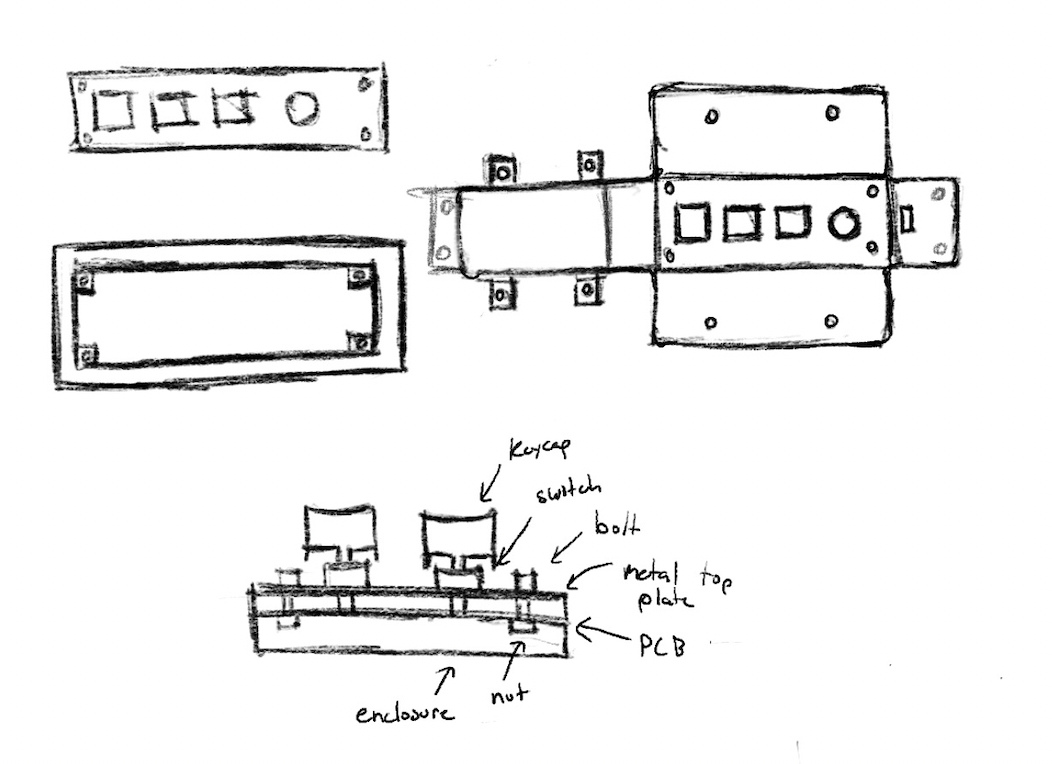
The initial design concept that the team landed on was that which used a water-jet cut aluminum enclosure that would be folded into shape. The case would house the PCB and Arduino that would connect to the standard MX Cherry style keyboard switches. There was some consideration for an under desk mounted design, but the tabletop concept was deemed more versatile.
initial Prototype
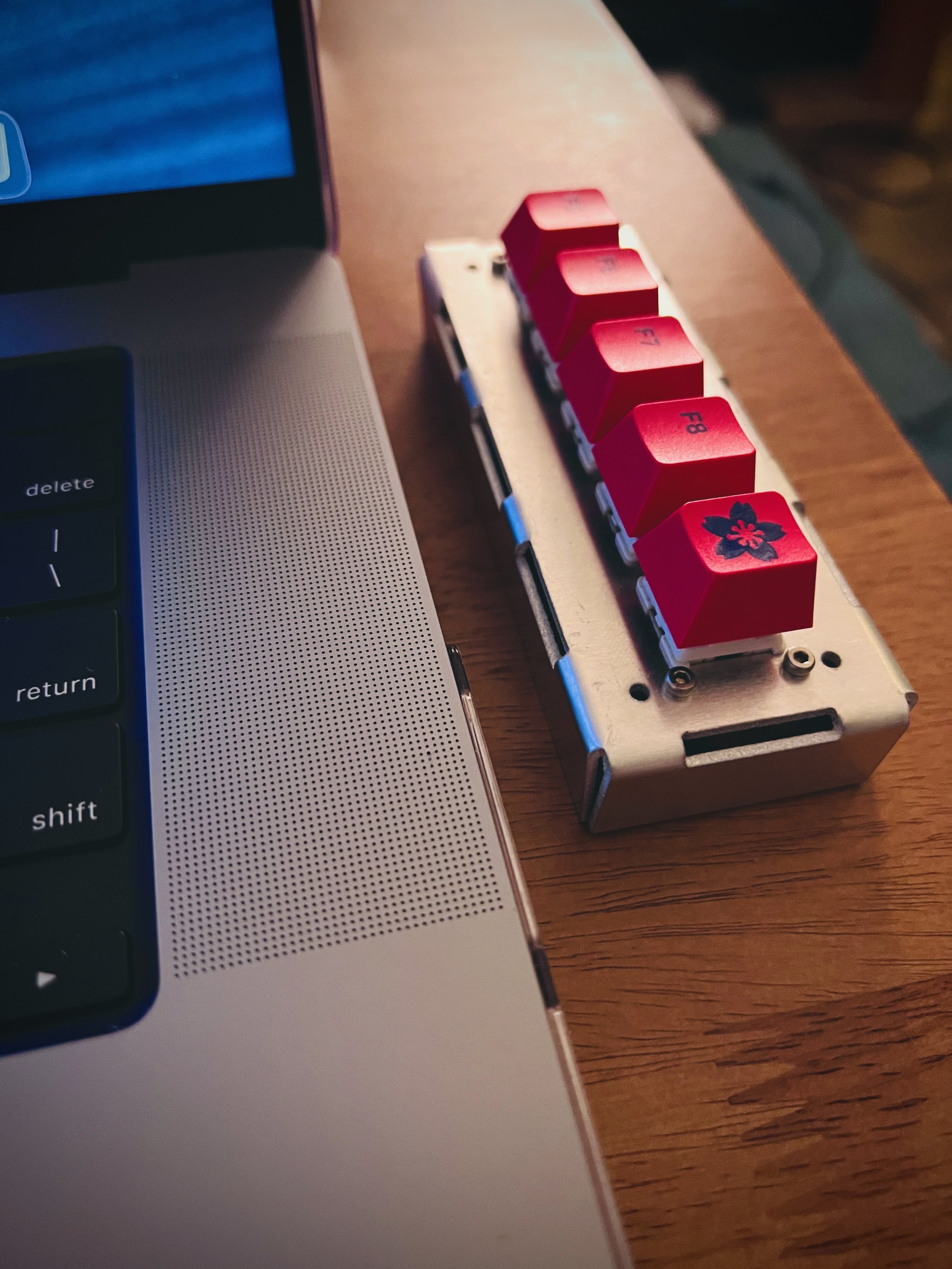

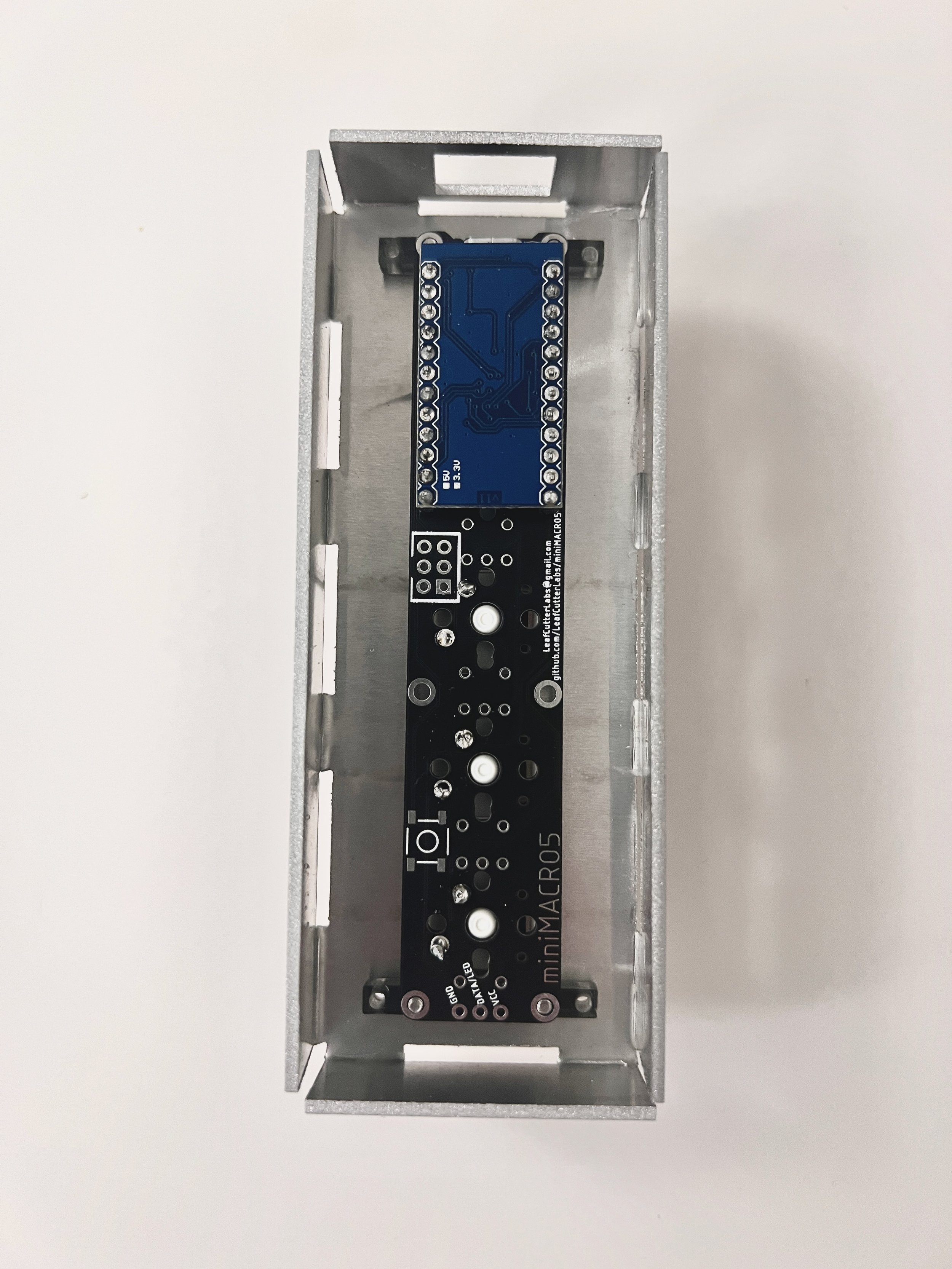
The initial prototype provided some useful lessons. Though the bend metal design gave it a unique industrial look that the team liked, the aluminum proved more difficult to work with than anticipated and meant that the bending process wasn’t as accurate as required. The electronics packaging and switch mounting was however proved to be viable and the produce was functional after flashing the Arduino with customized firmware.
The next steps would be to redesign the enclosure with different manufacturing techniques and to design a mold for producing custom keycaps.
DVT
Taking the lessons learned from the initial prototype the team moved to a new design using a stacked acrylic concept. Each layer is made out of clear laser cut 4mm acrylic and a 1.5mm aluminum sheet that the switches mount to. The keycaps themselves are cast using a silicon mold and have been colored with a gradient using different batches.
This design gives the unit a unique appearance that shows off the electronics packaging and accentuates the color choices made for both the aluminum plate and the keycaps.
Testing
Packaging
The packaging is an often overlooked aspect to product design yet provides some of the first interactions a user has with a product. It’s important to convey the messaging during those moments. The primary objective with to create a minimalist design that focuses on using recycled materials and places immediate attention to the unique design of our product.
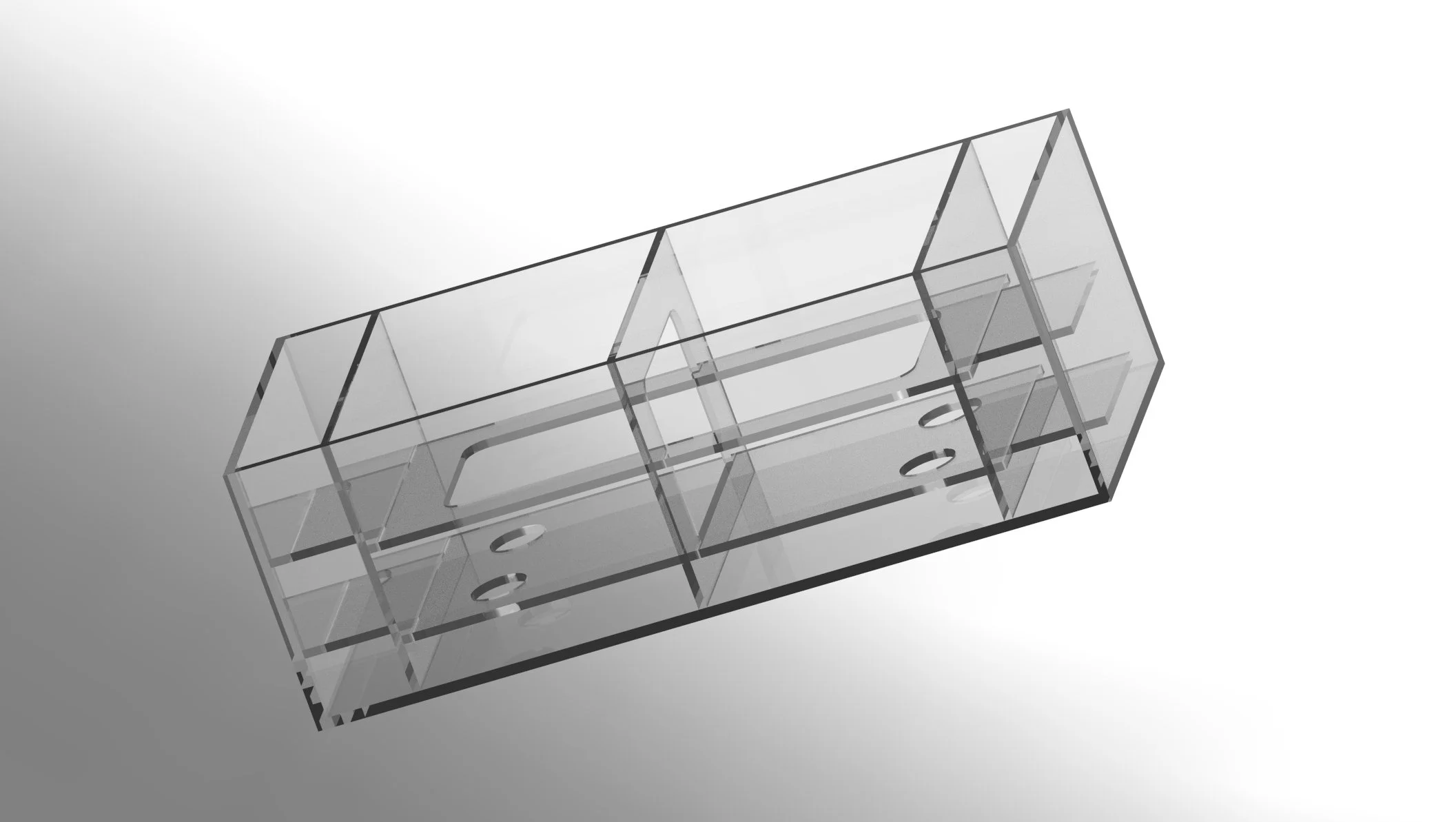
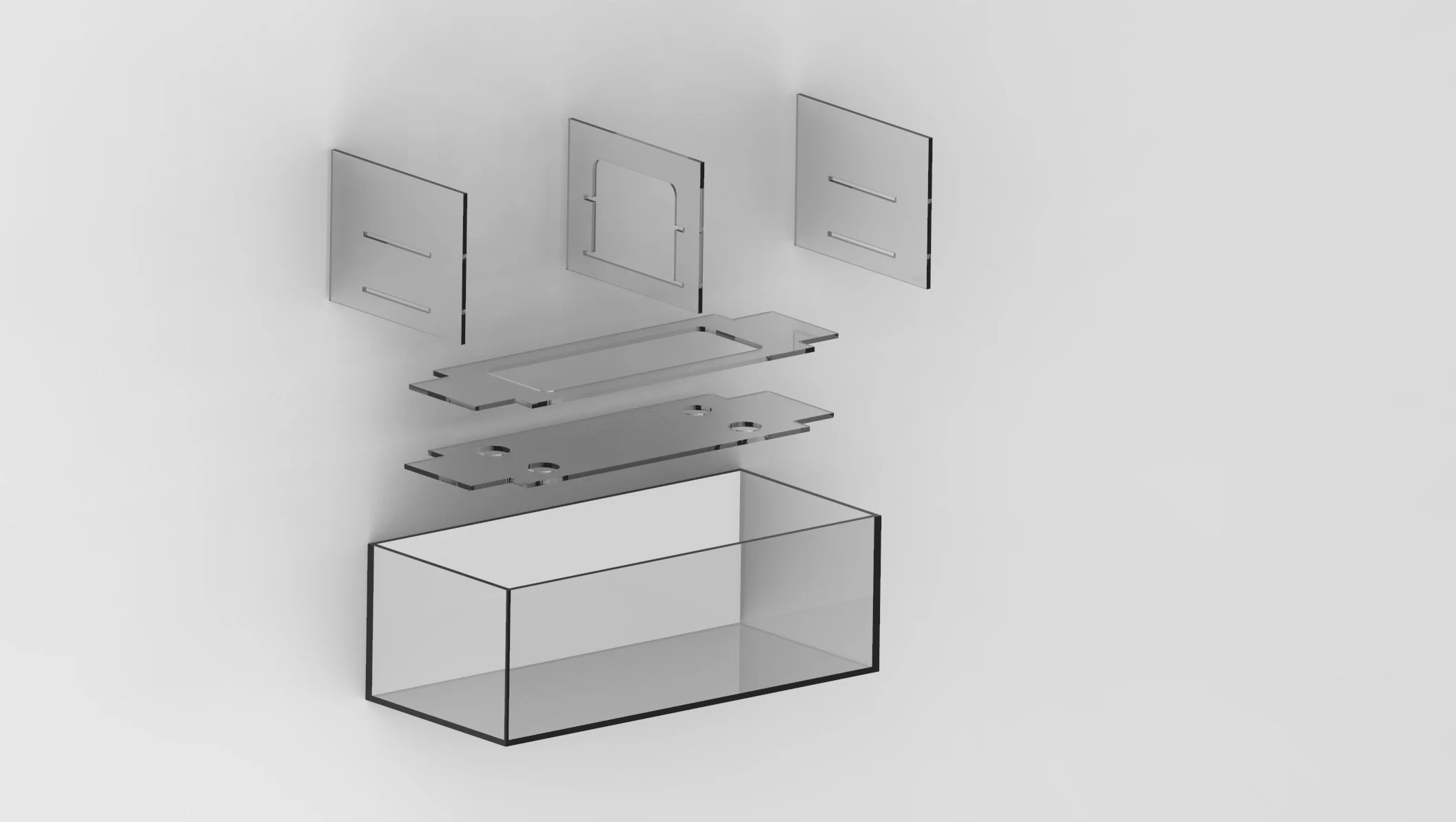




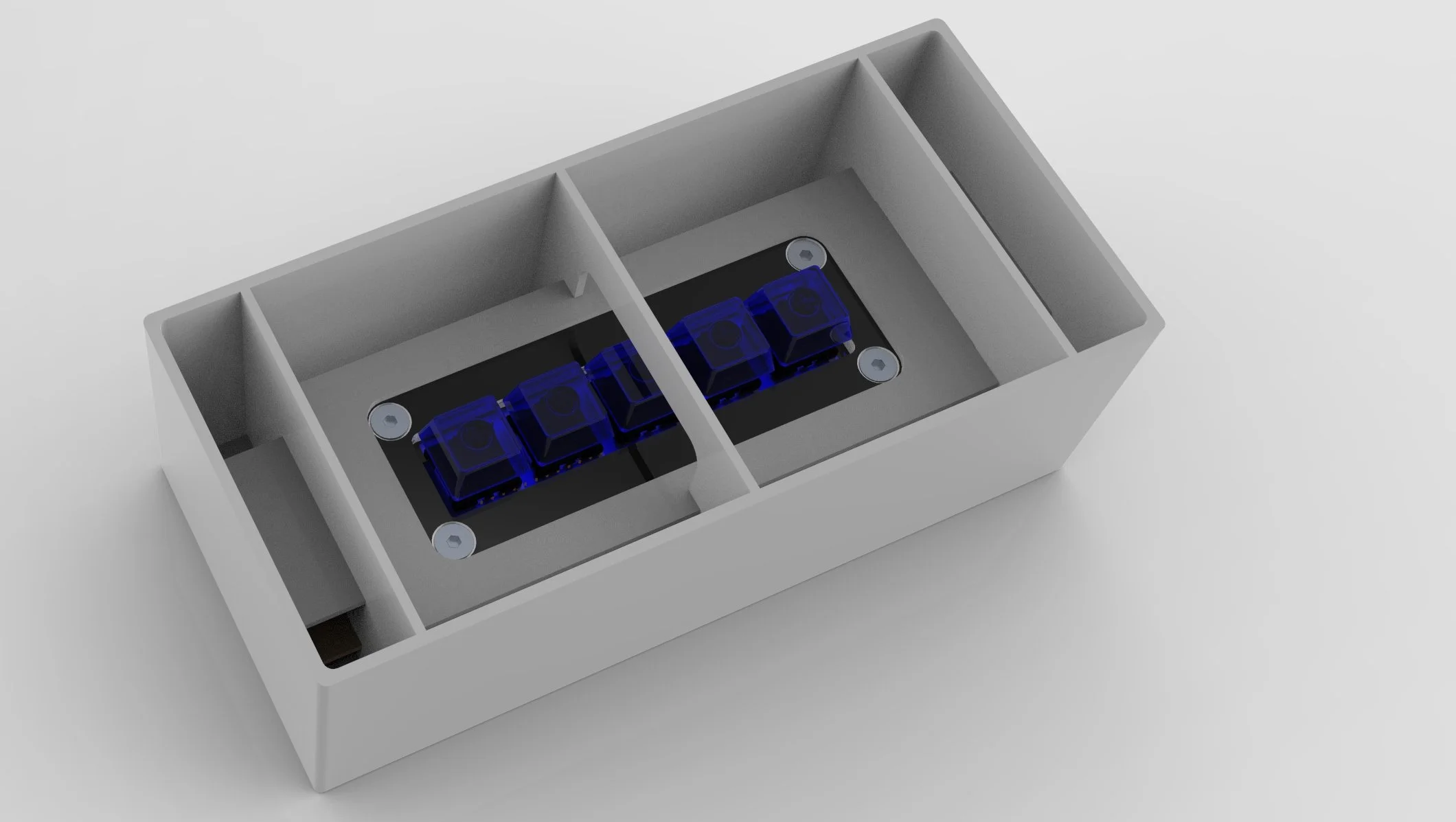

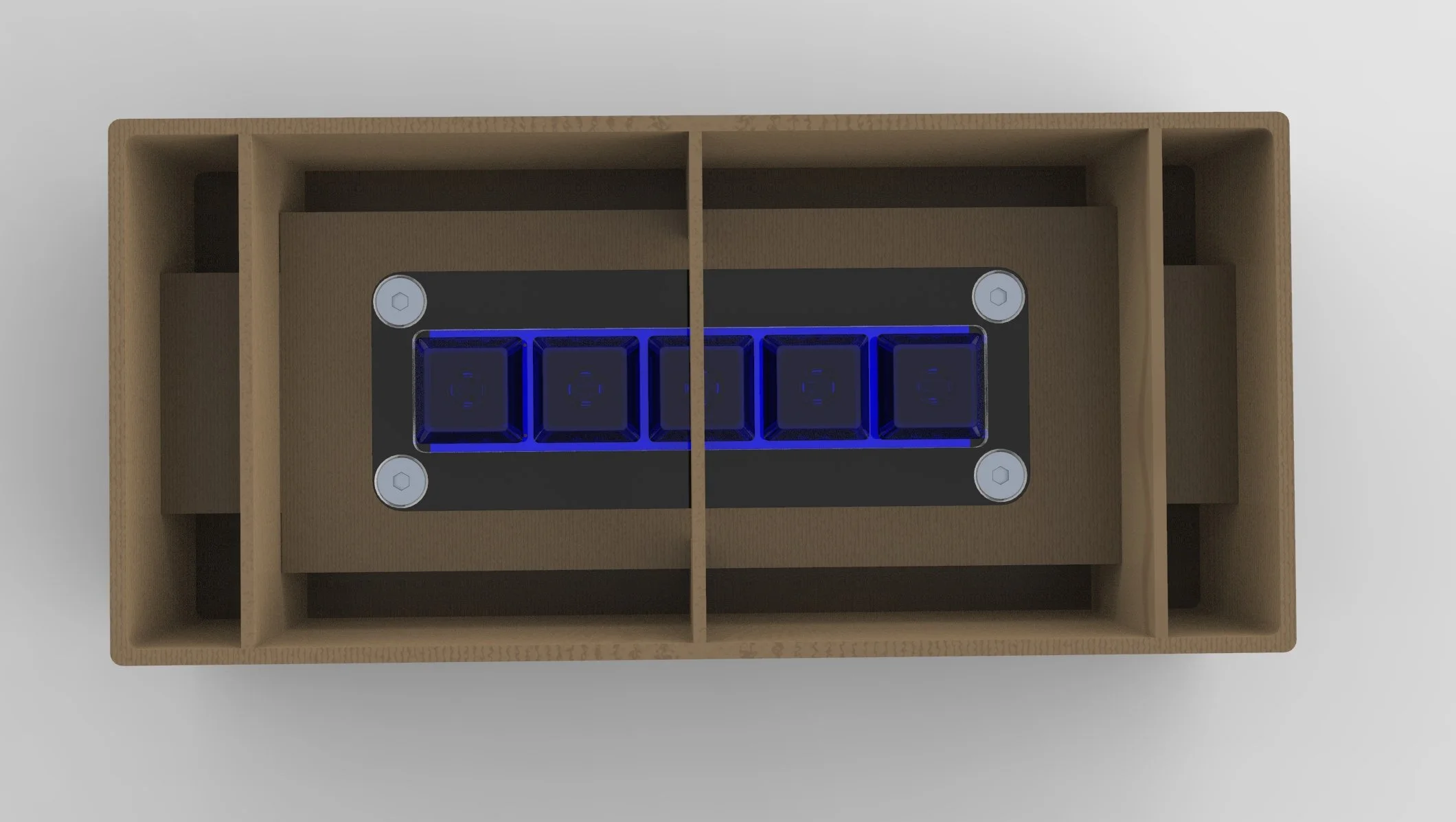
These renders show the finalized design and are rendered in clear in order to better show the internal geometry. The final packaging would use a solid recycled fiberboard for maximum strength. Designed with two primary horizontal components that sandwich the keyboard together in order provide protection during shipping. The vertical stabilizes slot into the horizontal plates and rest up against the sides of the box so the entire unit remains unified.
This design also reflects the stacked design language of the keyboard itself and puts the primary focus on the device as soon as the user opens the box. The design will hold the included USB cable wrapped up around one of the end posts of the horizontal plates, locking it in place during transport and providing an easy way to repack the device. The focus was on designing in a way that encourages the user to use the box as a carrying case when traveling, but also recyclable if no longer needed.
PVT
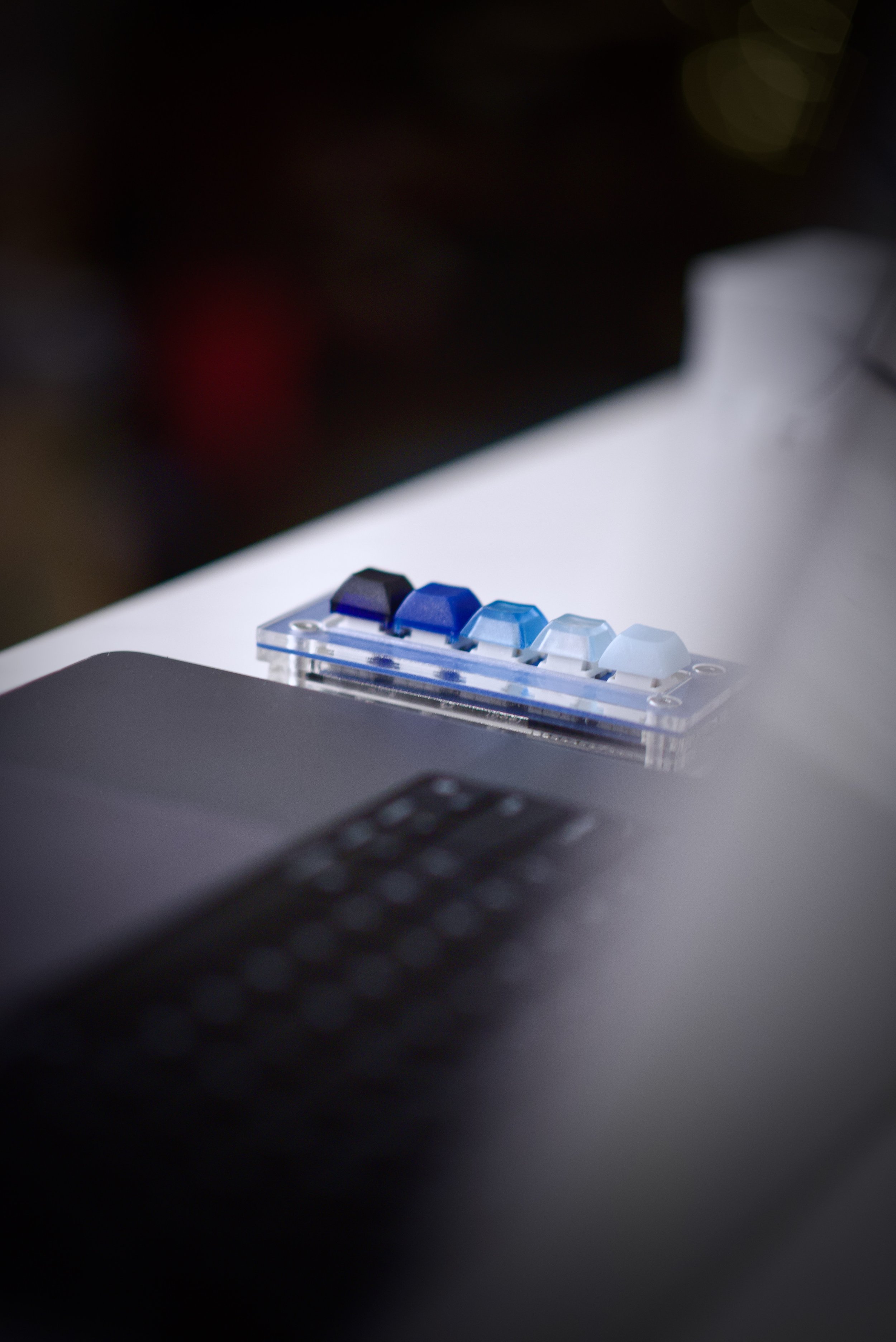
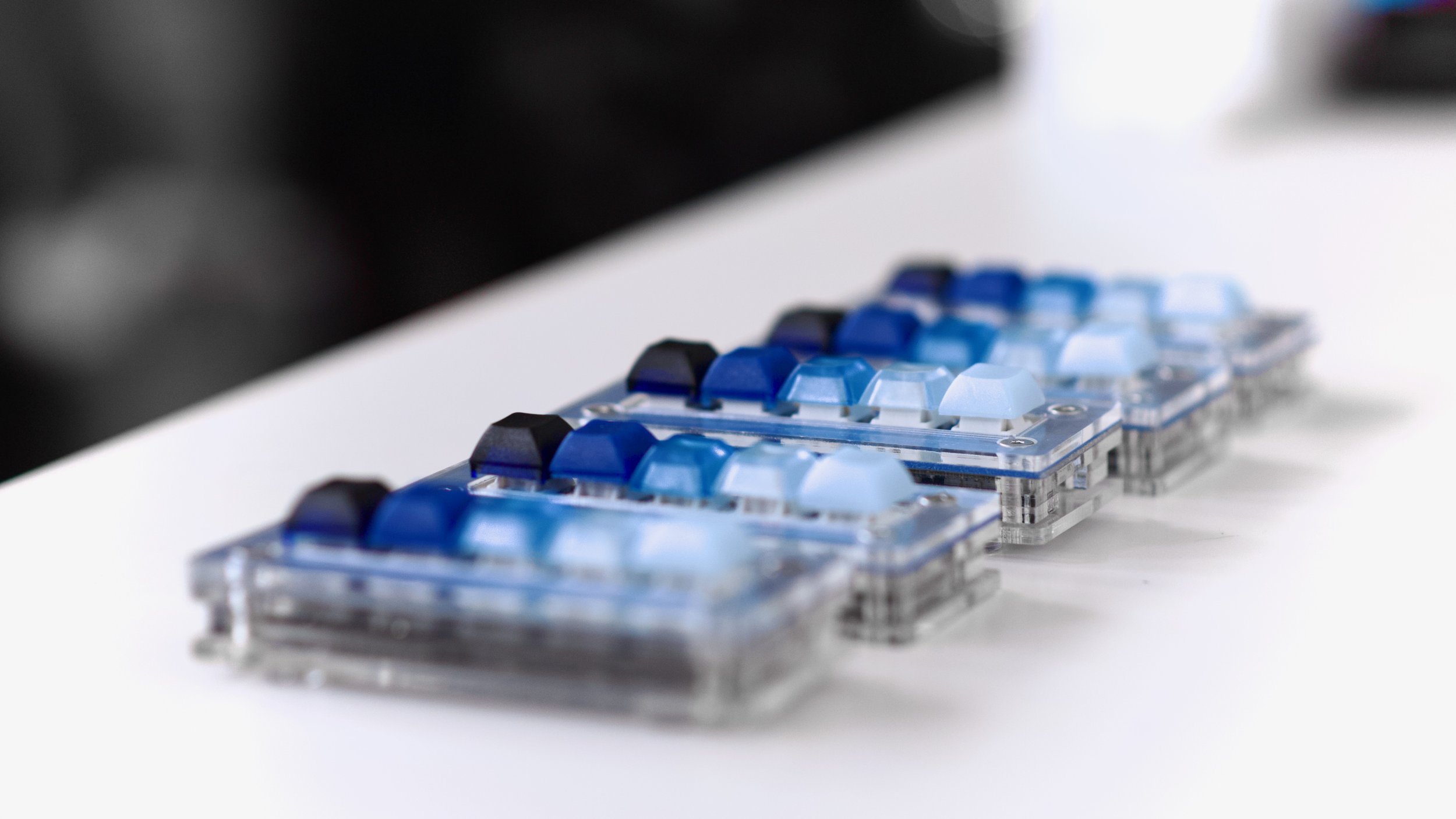
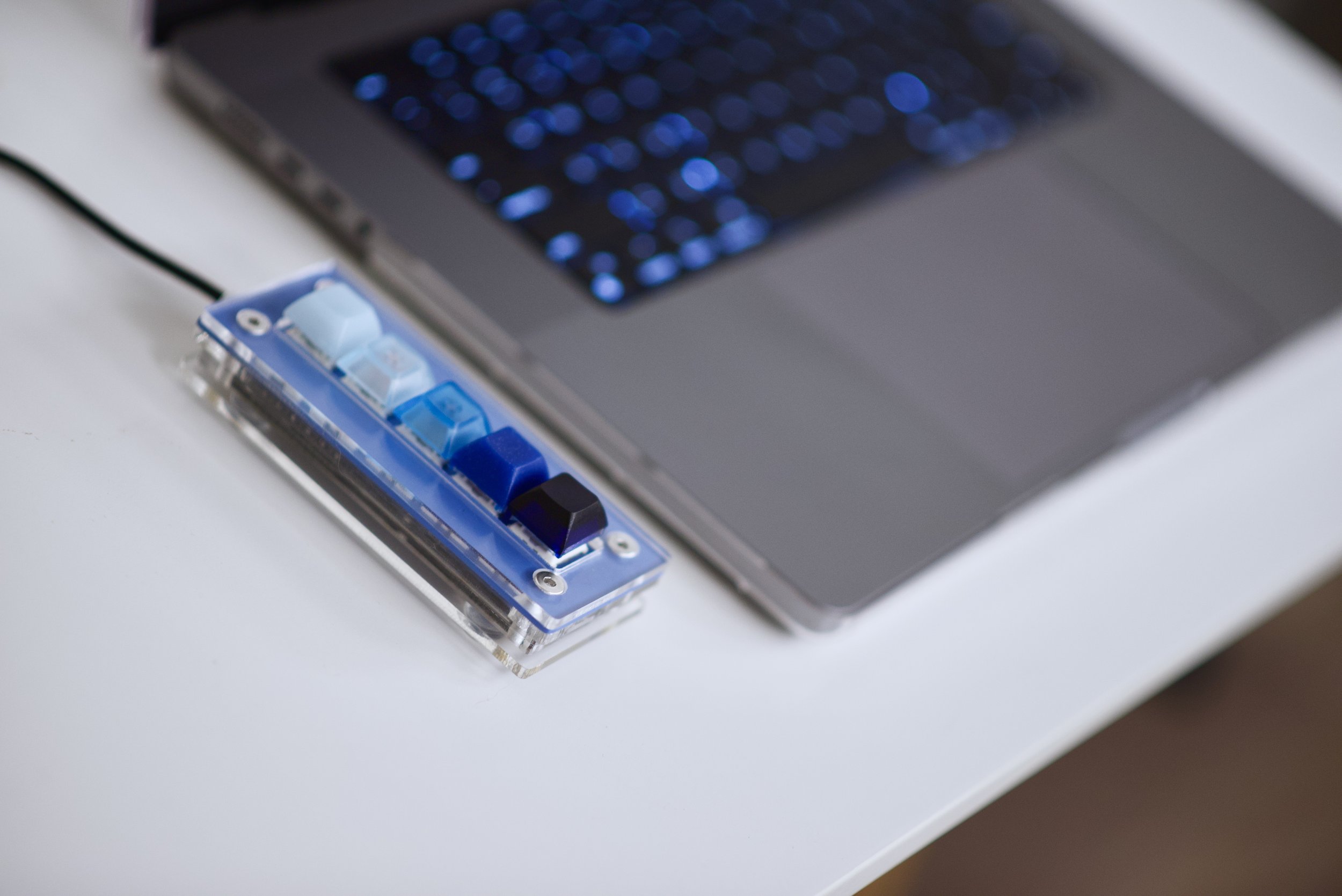
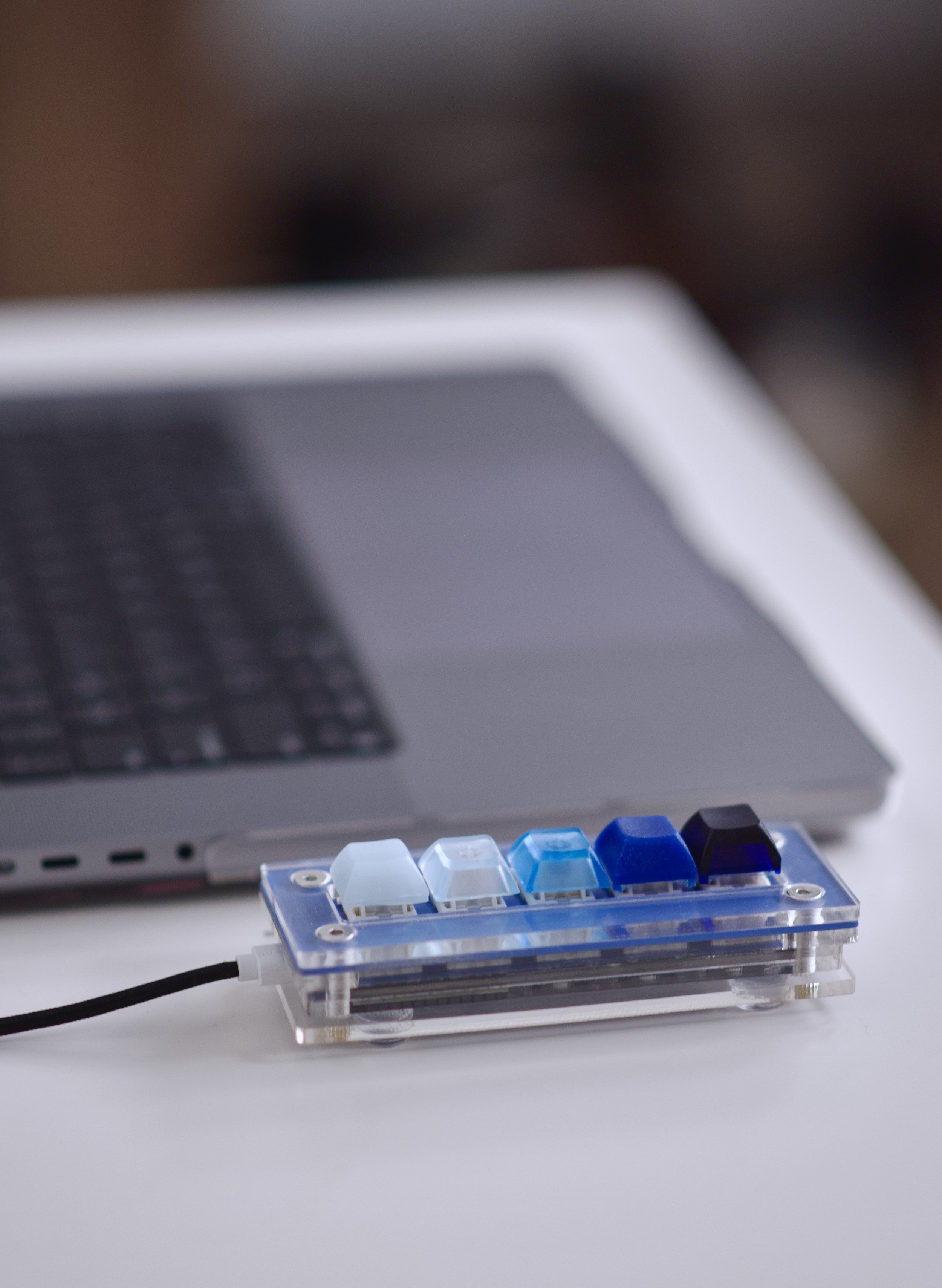
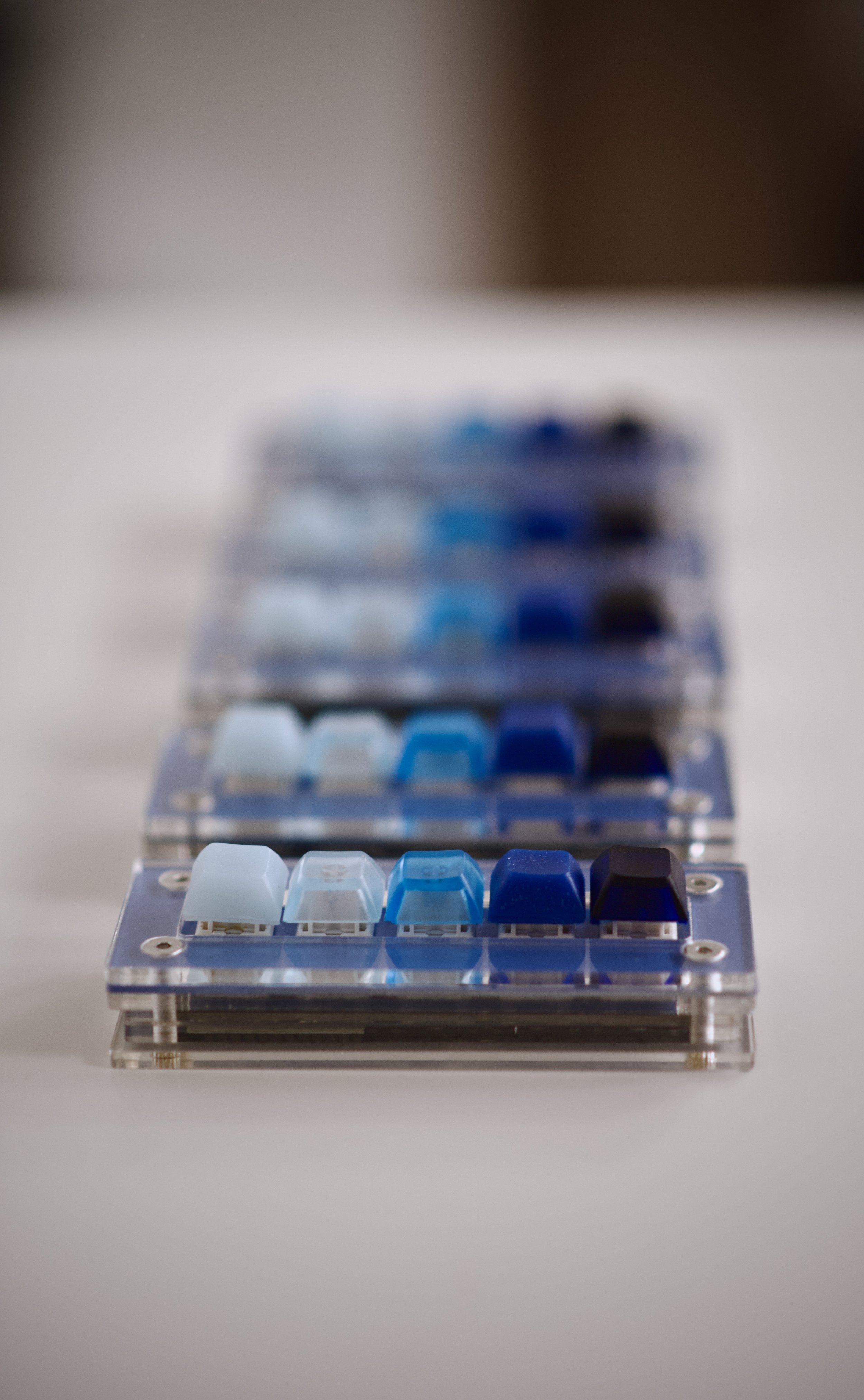
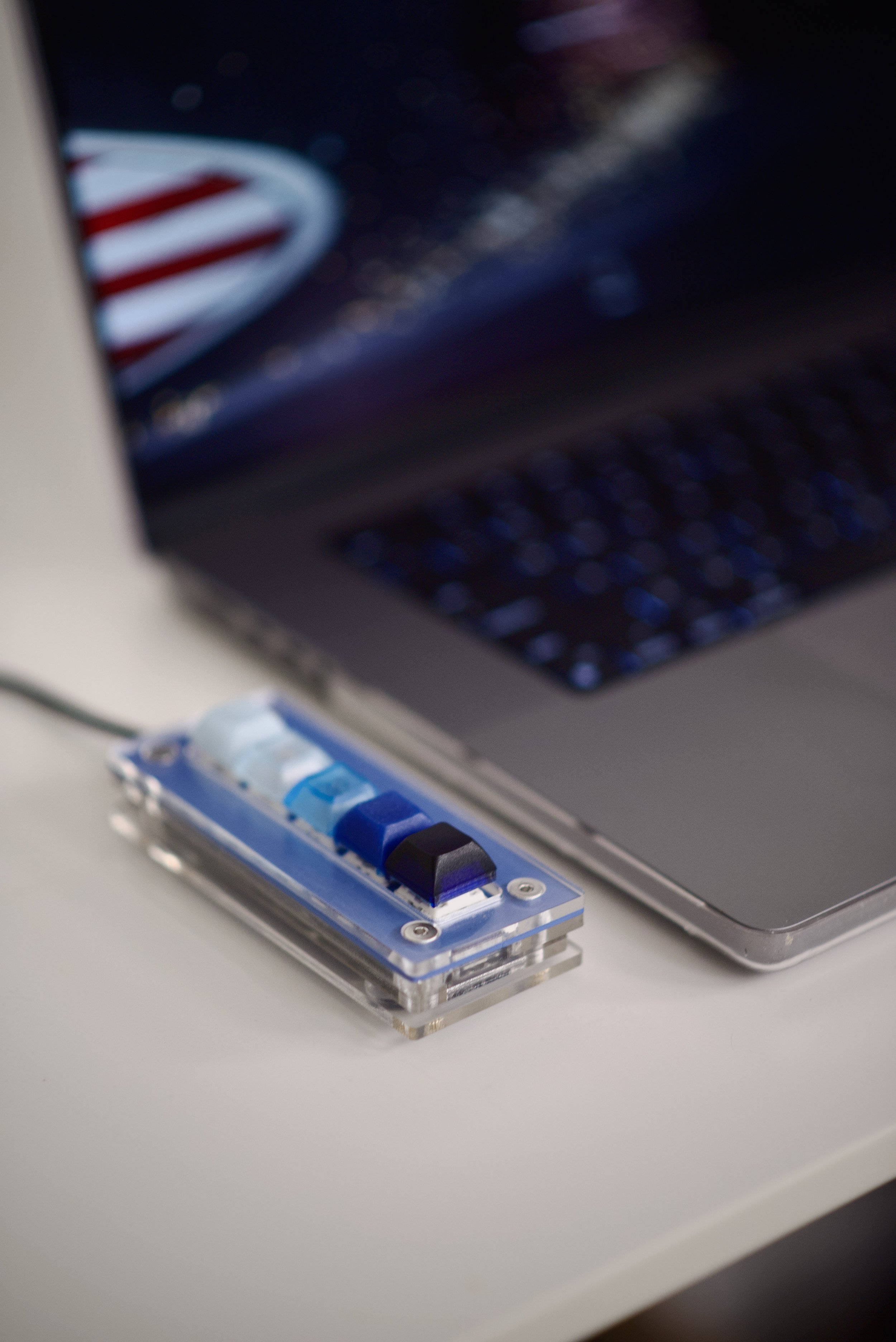
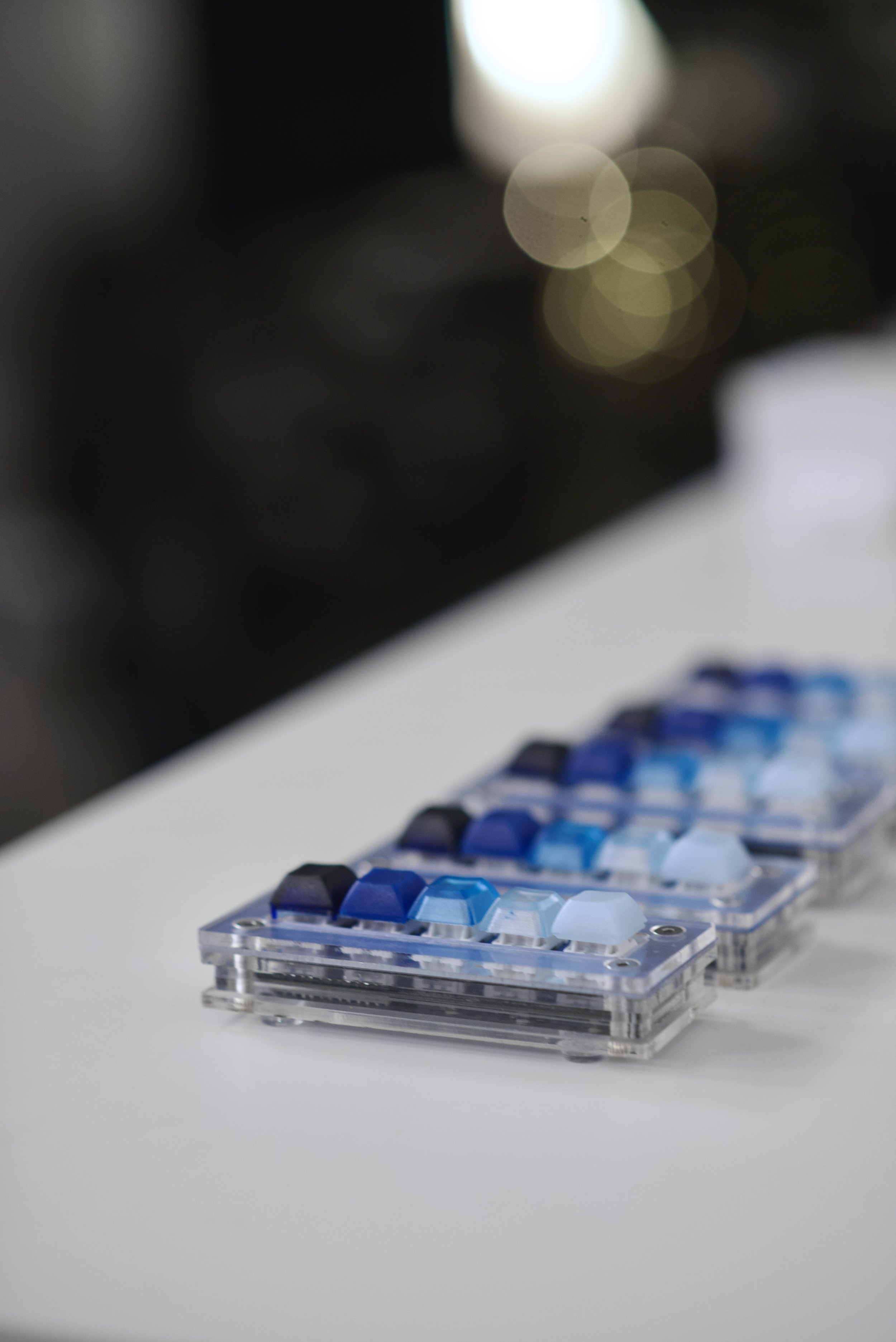
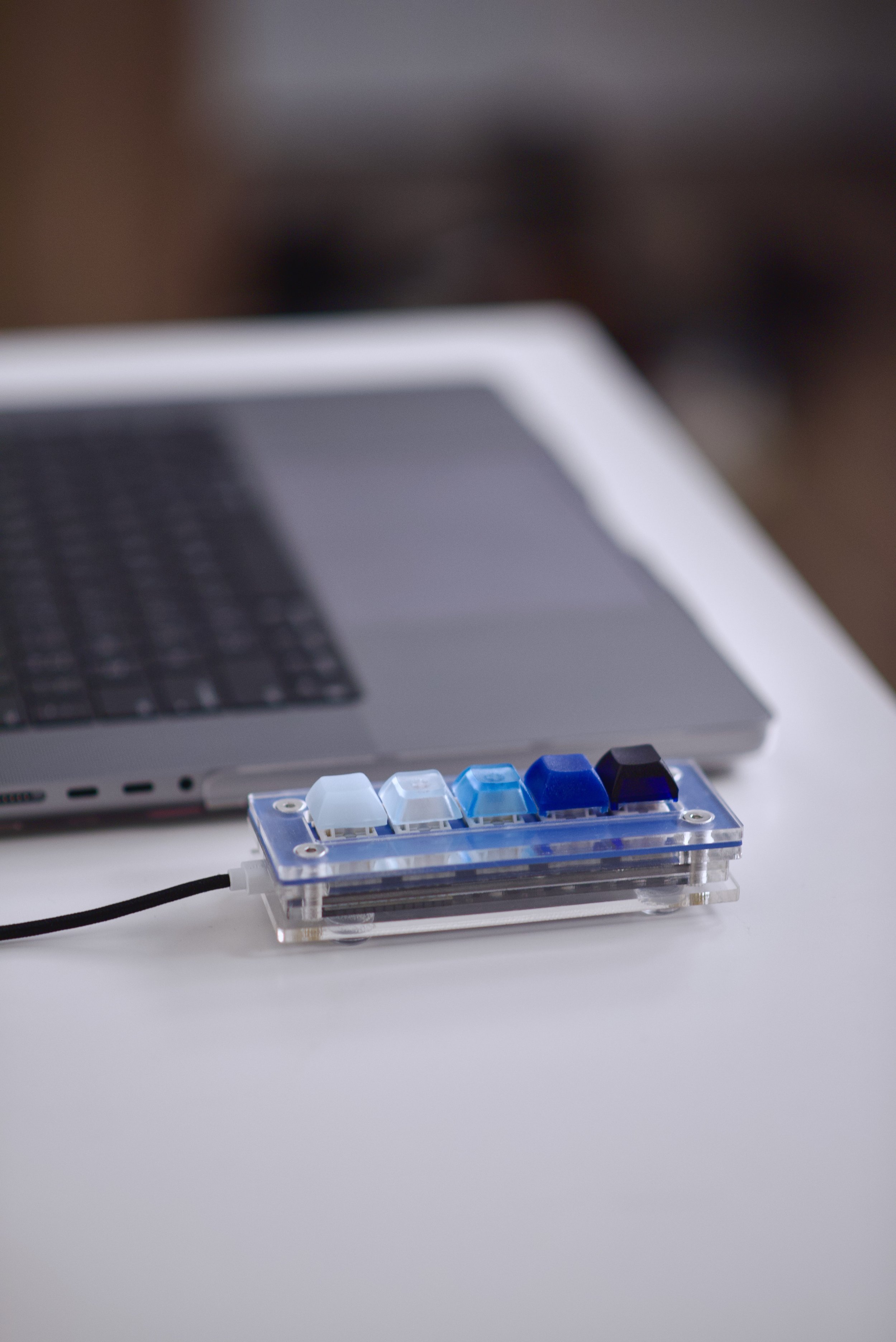
The PVT design further refined the overall concept with the use of thermoset threaded inserts on the bottom plate, allowing for a flush top plate for a cleaner appearance and better ergonomics. Five fully functional prototypes were made for this stage with custom firmware for customized button assignments.
Mass Production
The mass production design takes the PVT and utilizes an injection molded tub that replaces the stacked acrylic design. aPriori was used for manufacturing cost estimates and production feasibility. This design would use a custom PCB to further reduce the cost. Ultimately this mass production model would be easy to scale for large production and shows a realistic launch product.

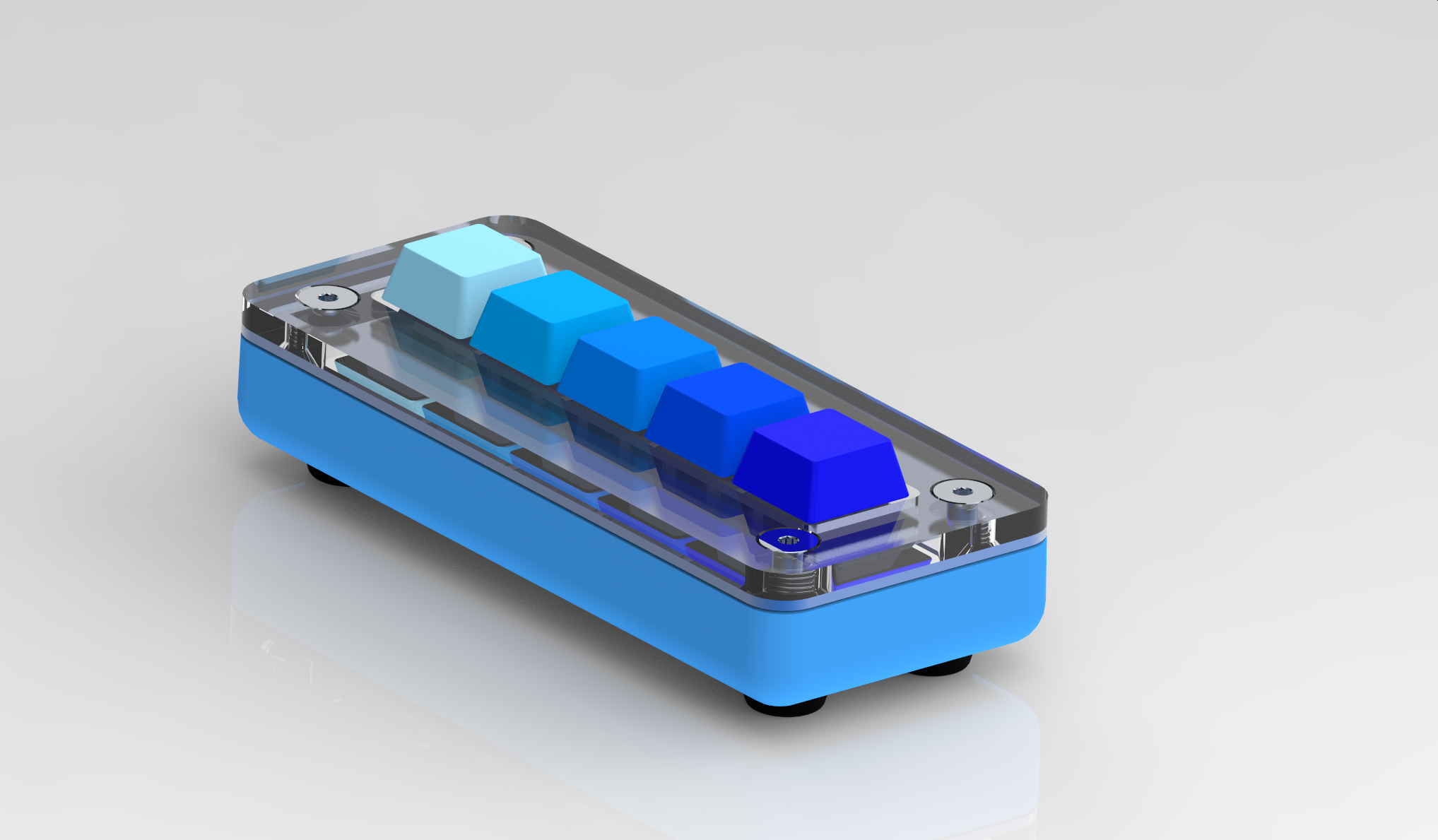


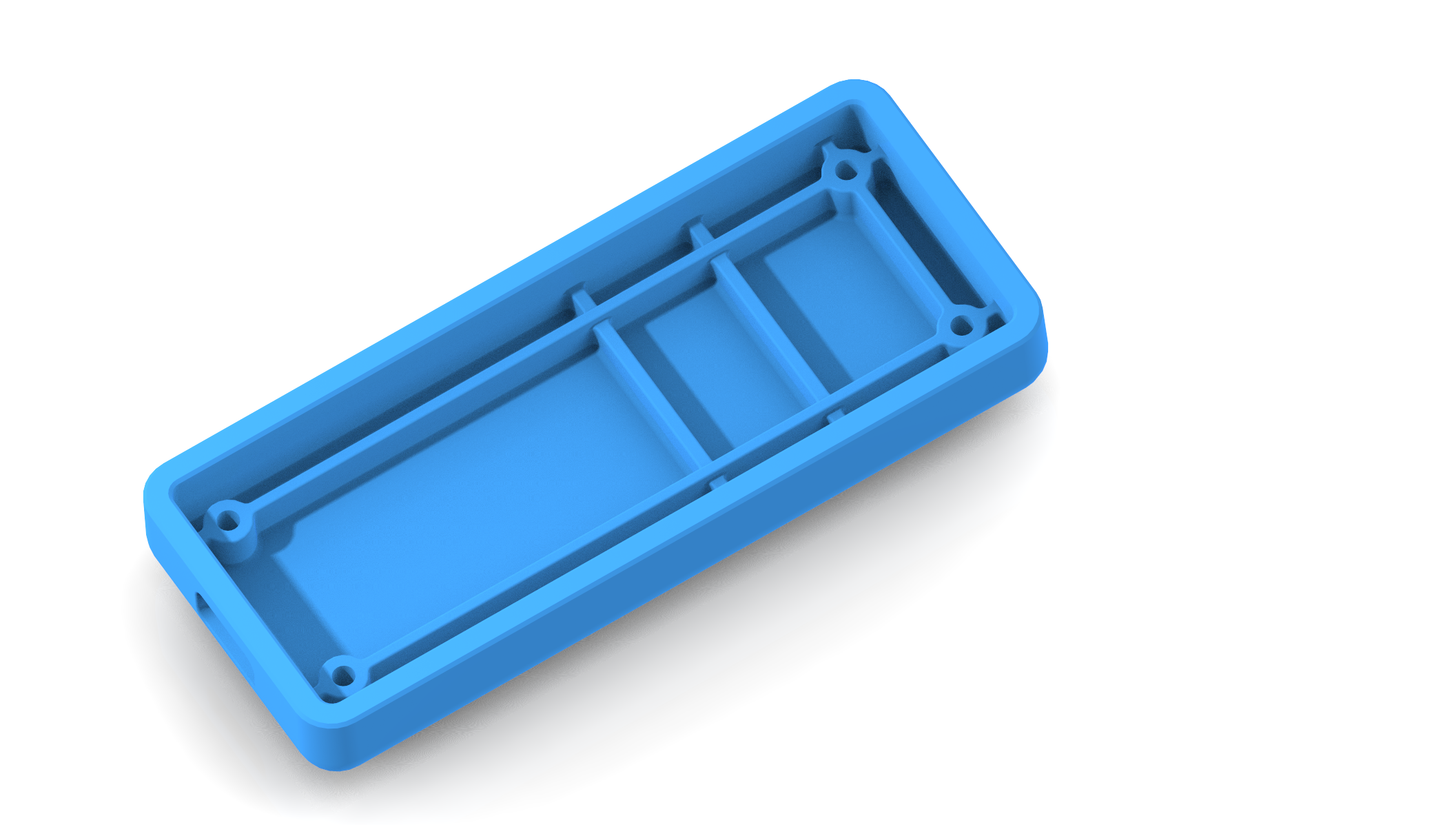


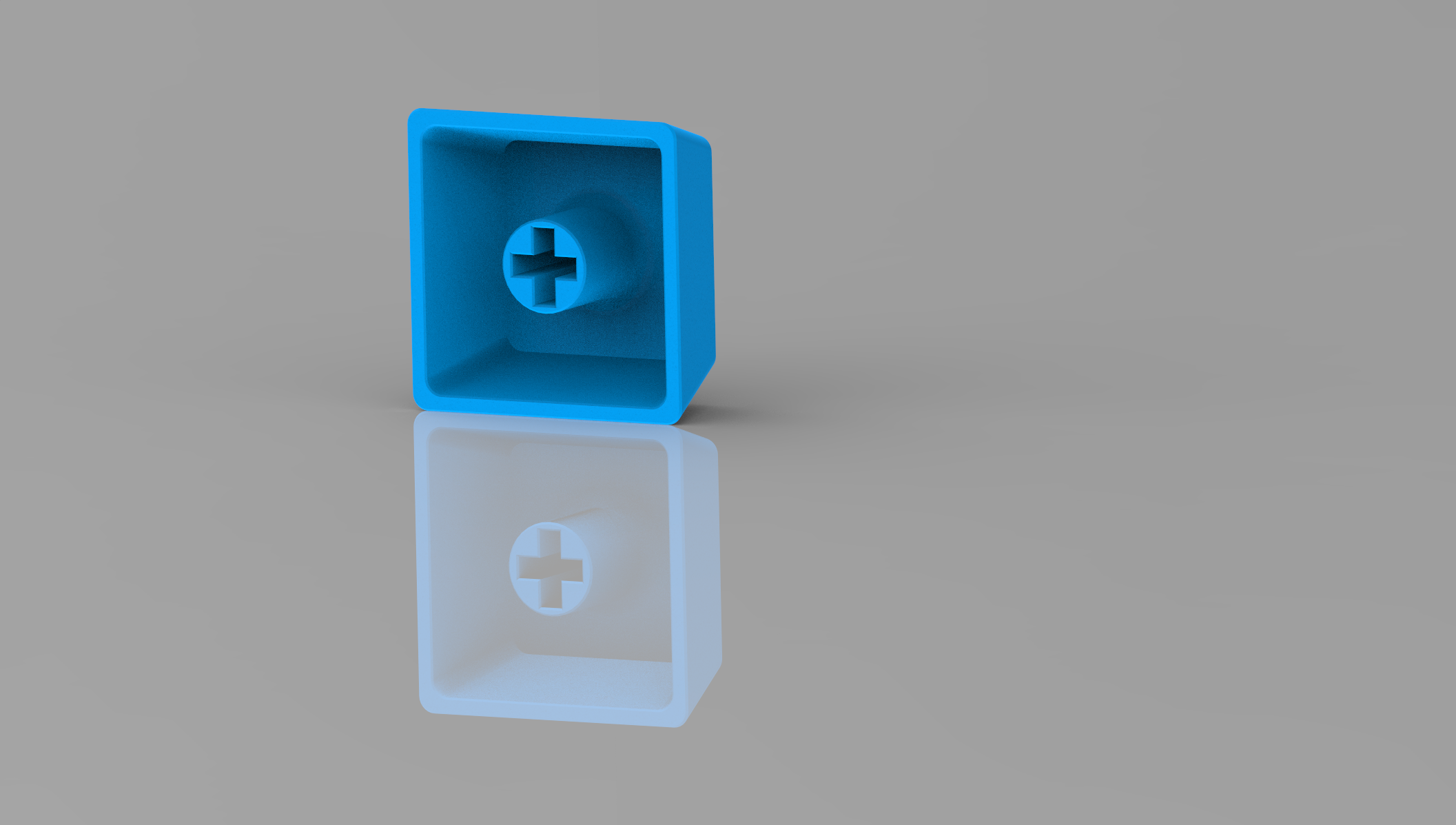
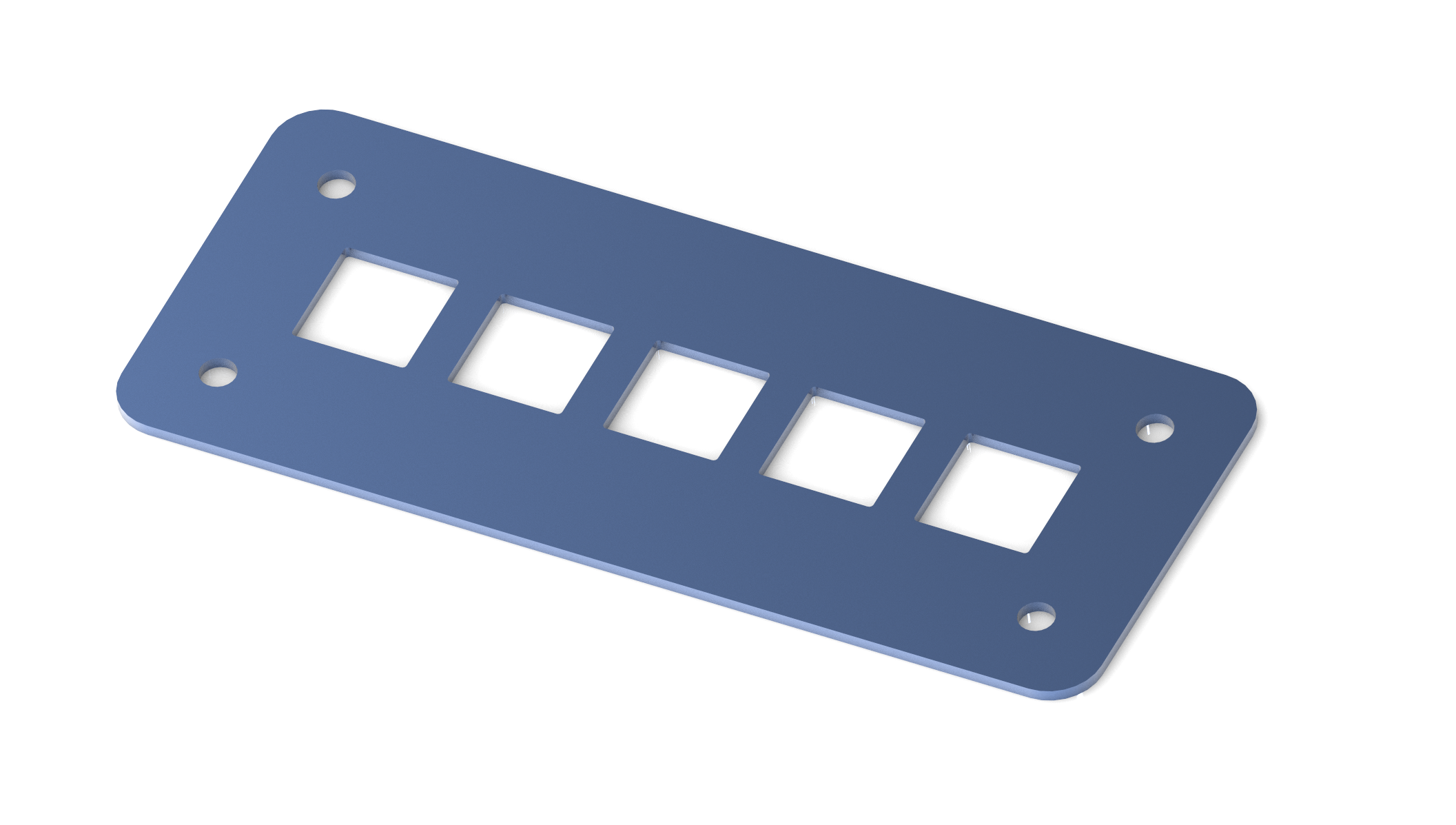
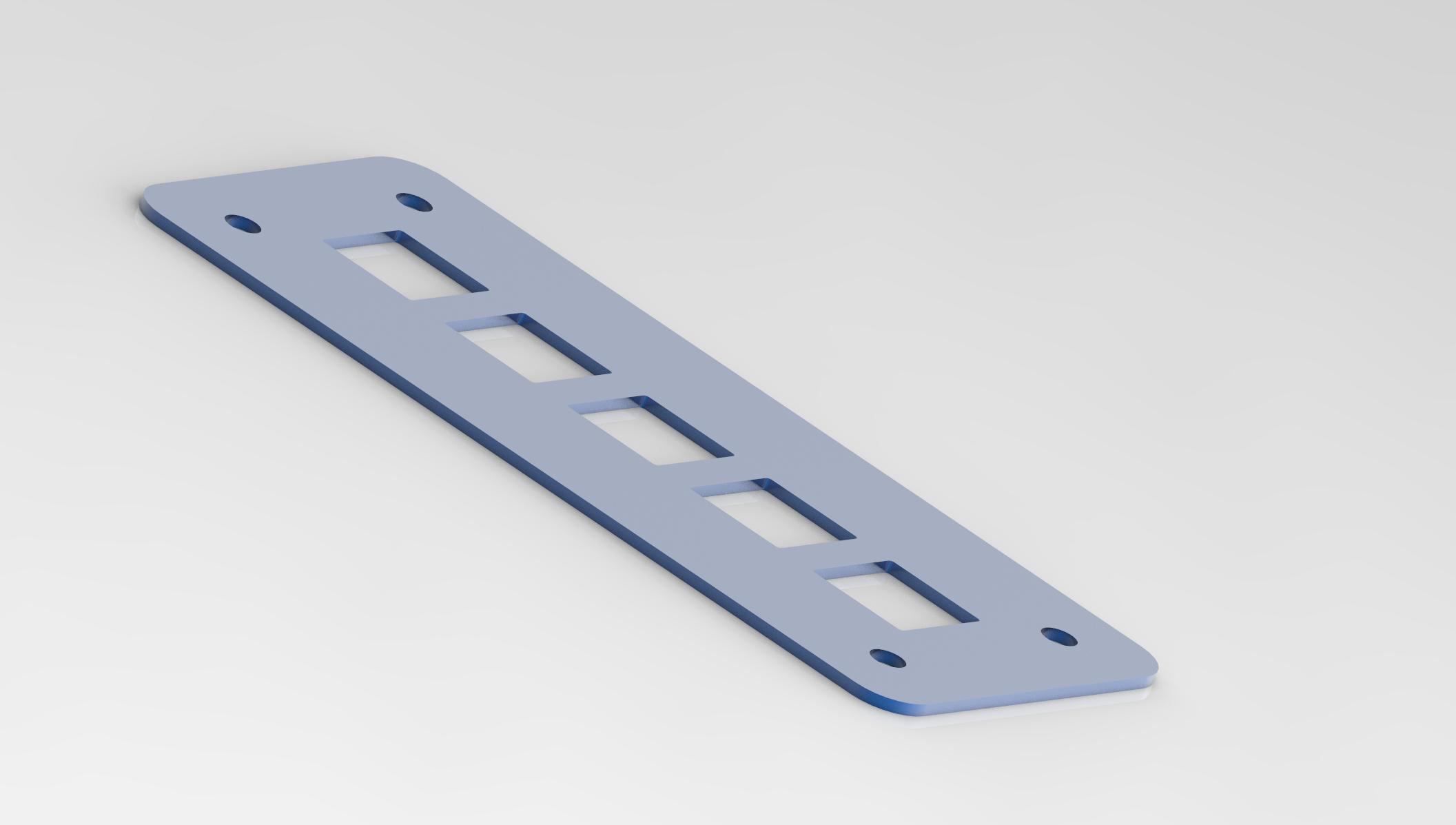